Car body design has come a long way since the early days of automotive engineering. We have witnessed a remarkable evolution in the materials and manufacturing processes used to create vehicle structures. From the sturdy steel frames of yesteryear to the cutting-edge composite materials of today, the quest for the perfect balance of strength, weight, and efficiency has driven innovation in what cars are made of.
Our journey through the history of car body design will take us from the wooden frames of the first automobiles to the steel revolution that dominated the 20th century. In this blog, we explore the shift towards aluminum for its lightweight properties and examine the groundbreaking impact of carbon fiber on structural integrity. Along the way, we will uncover how these changes in materials have shaped the automotive industry and what they mean for the future of vehicle design and performance.
From Wood to Steel: The Early Days of Car Design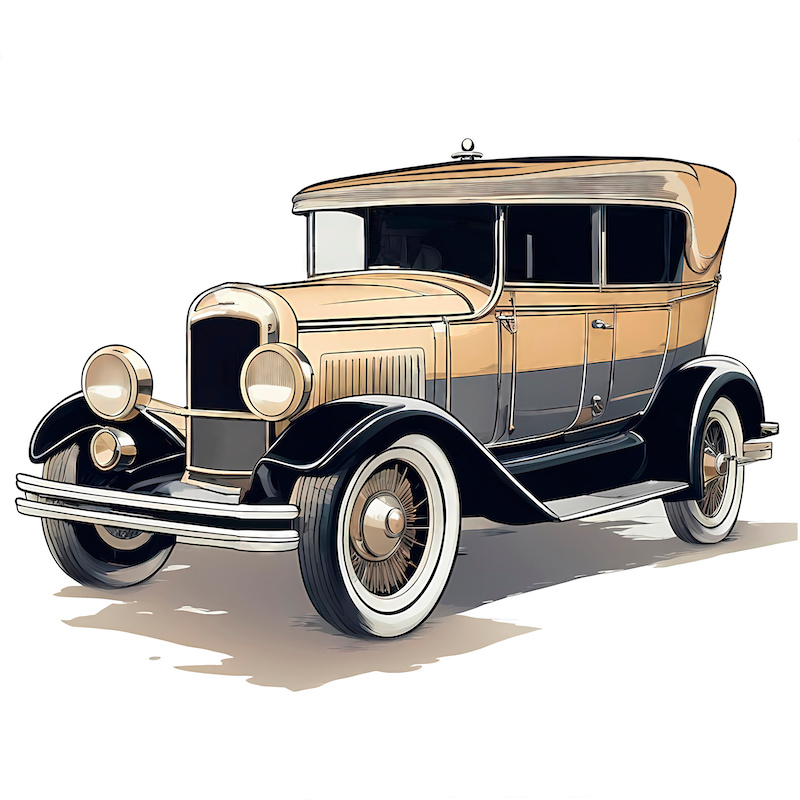
In the early 1800s, horse-drawn carriages were the main mode of transportation. When the idea of cars emerged in the 1890s, carriage makers applied their woodworking skills to create the first automobile bodies. These early cars were boxy and simple due to wood’s limited flexibility.
A significant shift occurred in 1914 when Dodge built the first all-steel-bodied automobile. This innovation was so successful that by the late 1930s, steel had become the primary material for most cars. Steel offered numerous advantages over wood, including greater strength, durability, and adaptability to mass production techniques.
The transition to steel marked a turning point in automotive engineering. It allowed for stronger, stiffer, and more durable bodies and chassis. Moreover, the ability to stamp and weld steel made it ideal for assembly line production, resulting in higher volume manufacturing at lower costs.
Aluminum Innovation for Car Design: Light-weighting for Efficiency
We have seen a significant shift in the automotive industry towards using aluminum for body panels and structures. This move has been driven by the need to improve fuel economy and reduce vehicle weight. Aluminum’s density is just one-third that of steel, making it an attractive option for carmakers looking to shed pounds.
Ford has been at the forefront of this aluminum revolution, betting heavily on what we call an “aluminum crash diet.” The results have been impressive, with aluminum-bodied vehicles showing up to a 29% boost in fuel economy. This weight reduction doesn’t come at the cost of safety or durability either. Aluminum’s flexibility allows it to absorb impact forces effectively, making it an excellent choice for crash structures.
However, the switch to aluminum isn’t without its challenges. It is more expensive than steel, both in raw material costs and manufacturing processes. This can lead to a 60-80% cost premium for aluminum cars. Additionally, some users have reported issues with paint adhesion and premature corrosion in aluminum vehicles.
The Carbon Fiber Revolution: Strength Meets Lightness in Car Design
We have seen a remarkable shift in automotive engineering with the introduction of carbon fiber composites. These materials, made of carbon fibers embedded in a polymer matrix, offer an exceptional strength-to-weight ratio. By using carbon fiber, we can reduce a car’s weight significantly, leading to better fuel efficiency and lower emissions. In fact, a 10% weight reduction can result in a 7% decrease in fuel consumption.
Carbon fiber parts aren’t just lightweight; they are also incredibly strong and stiff. They have the highest strength and stiffness per density on the market, making them ideal for creating safer, more durable vehicles. These components can absorb energy at a higher rate, which is crucial in the event of a crash.
Despite these advantages, the adoption of carbon fiber in automotive design has been slow due to cost and manufacturing challenges. However, as technology advances and production scales up, we are seeing more widespread use of this revolutionary material in the automotive industry.
Whatever your car is made of, we would love to help you maintain it. If you live in the San Gabriel Valley, swing by and show us your wheels.
About DG Collision Center, an Auto Body Shop in Covina, California
We would love to help restore your vehicle following a car accident or comprehensive damage. DG Collision Center in Covina, California is your one-stop-shop in Covina for auto body repair after car accidents. Our highly trained team includes specialized technicians. We work directly with all insurance companies. This enables our customers to file a claim without even needing to be present.